The process of manufacturing glass has long posed a challenge to our environment, releasing a staggering 86 million tons of carbon dioxide worldwide each year.
In a remarkable turn of events, researchers at Penn State have stumbled upon a new type of glass that challenges the very foundations of glass’s fragility.
Named LionGlass after Penn State’s Nittany Lion mascot, this innovative glass has showcased an exceptional resistance to cracking that has left scientists astounded.
Glass, known for its brittleness, has long been perceived as a delicate material that succumbs easily to pressure.
However, LionGlass defies this perception by displaying a resistance so formidable that even a one kilogram-force load from a Vickers diamond indenter couldn’t crack it.
This unexpected strength has set LionGlass apart as a material that pushes boundaries and shatters preconceived notions.
To put LionGlass’s resilience into perspective, it’s important to consider the common soda lime glass that we encounter in everyday items.
While soda lime glass shows signs of cracking under a load of around 0.1 kilograms force, LionGlass maintains its integrity with a remarkable 10 times higher crack resistance.
This remarkable feat, however, posed a challenge to the researchers themselves, as their equipment struggled to measure LionGlass’s unmatched strength to its full extent.
Nick Clark, a postdoctoral fellow in Professor John Mauro’s lab, expressed their surprise and the equipment’s limits, stating, “We kept increasing the weight on LionGlass until we reached the maximum load the equipment will allow. It simply wouldn’t crack.”
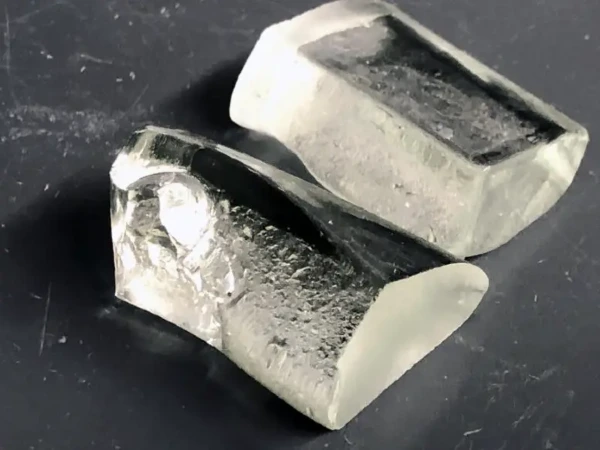
This unanticipated discovery highlights the inherent curiosity of scientific exploration and the potential for breakthroughs in unexpected places.
The significance of this newfound resilience in LionGlass extends far beyond its scientific novelty. In the realm of glass, the formation of microcracks along the surface often signifies the beginning of its weakening.
These microcracks serve as vulnerabilities that lead to eventual failure.
However, LionGlass challenges this norm by displaying a remarkable resistance to microcrack formation, redefining how glass withstands wear and tear.
While LionGlass’s breakthrough may evoke images of extraordinary strength, its applications are where its potential truly shines.
Industries such as automotive, electronics, architecture, and communication technology stand to benefit from a material that defies conventional fragility.
Even sectors like health care, where preservation is paramount, could find value in LionGlass’s superior strength and chemical resistance.
The breakthrough in LionGlass’s resilience holds the promise of a brighter, more sustainable future in the realm of glass production.
Professor John Mauro envisions that the newfound strength of LionGlass could pave the way for lighter and more eco-friendly products.
With LionGlass demonstrating an astonishing 10 times greater resistance to damage compared to conventional glass, the possibility of producing significantly thinner products comes to the forefront.
By reducing the thickness of glass while maintaining the same level of damage resistance, Mauro believes that the potential benefits are manifold.
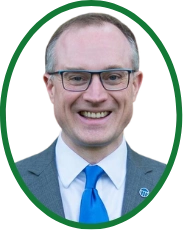
Meet Dr. John Mauro
Dr. Mauro is an accomplished figure in the field of glass science and engineering, with a Doctorate in Glass Science from Alfred University. His career began at Corning Inc. in 1999, where he held various roles, including senior research manager of the Glass Research department. Dr. Mauro's contributions to Corning include inventing or co-inventing multiple glass compositions, most notably for Corning Gorilla® Glass products. In 2017, he joined The Pennsylvania State University as a professor of Materials Science and Engineering.
The implications stretch beyond just material efficiency. Lighter-weight LionGlass products translate into less consumption of raw materials during manufacturing, ultimately contributing to a more eco-conscious production process.
Additionally, the transportation of these lighter glass products would demand less energy, thereby creating a ripple effect of reduced carbon emissions.
As Mauro emphasizes, “It’s a winning situation for everyone.” The potential of LionGlass to not only redefine glass’s physical attributes, but also its environmental impact aligns with the global drive towards sustainability.
The familiar soda lime silicate glass, found in our everyday essentials, depends on melting three primary components: quartz sand, soda ash, and limestone.
However, the pivotal twist lies in soda ash and limestone, both culprits behind releasing carbon dioxide (CO2), a greenhouse gas, when they’re subjected to the melting process.
Delving deeper, LionGlass addresses this environmental concern on two fronts. Firstly, it slashes down the release of CO2 by sidestepping the use of carbon-releasing materials. Secondly, the magic happens during the glassmaking process itself.
LionGlass ushers in a transformation by lowering the melting temperatures by a remarkable 300 to 400 degrees Celsius.
This groundbreaking feat translates to an astonishing 30% drop in energy consumption compared to the conventional soda lime glass.
While LionGlass’s exceptional strength has garnered attention, its journey is far from over.
Professor Mauro affirms, “Our mission is to ensure glass manufacturing becomes sustainable for the long haul.”
LionGlass ushers in a new era by eliminating the use of carbon-containing materials during its production process.
What’s more, it significantly reduces the melting temperature of glass, which in turn translates to less energy consumed.
More To Discover
- Vietnam’s Floating Bamboo House: A Lifeline Against Rising Seas
- The Rising Energy Demand of AI and Data Centers: Is It That Bad?
- UK’s Chicken Industry in Crisis: 80 Million Deaths Point to Unsustainable Practices
- FTC Report: Grocery Stores Boosting Profits, Driving Up Food Prices While Falsely Blaming Inflation, Supply
Reflecting on the legacy of glassmaking, Mauro acknowledges the critical role glass has played in shaping modern civilization:
“Humans learned how to manufacture glass more than 5,000 years ago and since then it has been critical to bringing modern civilization to where it is today,” Mauro said. “Now, we are at a point in time when we need it to help shape the future, as we face global challenges
such as environmental issues, renewable energy, energy efficiency, health care, and urban development. Glass can play a vital role in solving these issues, and we are ready to contribute.”
Today, as our world grapples with pressing challenges like environmental concerns, renewable energy, energy efficiency, healthcare, and urban development, glass is poised to once again emerge as a solution.