Scientists are on the verge of a breakthrough in textile recycling, addressing a significant challenge in the industry. Elastane, the material that makes your running tights fit so well, is a blessing for comfort but a curse for recycling. When elastane is mixed with other fibers like cotton, wool, or nylon – a common practice in today’s clothing – it becomes nearly impossible to recycle these fabrics. The difficulty lies in separating the different fibers.
The impact of this challenge is evident in recycling statistics. In Denmark, for instance, only about 6% of discarded clothes are recycled. This is a stark contrast to the 32% recycling rate for plastic packaging in the country.
However, a team led by Assistant Professor Steffan Kvist Kristensen at Aarhus University’s Interdisciplinary Nanoscience Center may turn the tide. They’ve developed a new technology capable of separating fibers in mixed fabrics. This groundbreaking work, published in the journal Green Chemistry, focuses on efficiently removing elastane from nylon.
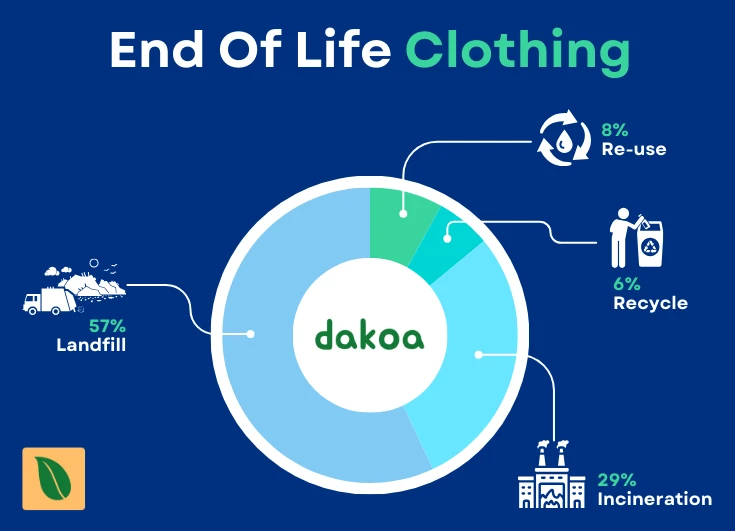
Kristensen explains the significance of their work: “We’ve developed a method to remove elastane completely from nylon. We’re not quite there yet with cotton, because some of the cotton fibers are broken down in the process. But we believe that, with some minor adjustments, we can solve this problem.” He adds, “In other words, we can disassemble the fabric so that we can recycle far more textiles in the future.”
This innovation could revolutionize the textile recycling industry, dramatically increasing the amount of fabric that can be reused and reducing the environmental footprint of clothing disposal.
A New Method to Break Down Mixed Fibers
Separating elastane from other fibers in clothing is challenging. Clothes are typically made by wrapping main fibers like nylon or cotton around elastane fibers, which are long chains of molecules. Assistant Professor Steffan Kvist Kristensen explains the complex process: “The fibers only break apart if we break the long chains of molecules.”
The team at Aarhus University has developed a method involving high heat and a specific alcohol to break down elastane. “The many links in the elastane chain are bound together by a small molecule called a diamine. By heating the clothes to 225 degrees Celsius and adding a specific alcohol, we have found a method to break down the bonds in elastane. When this happens, the chains fall apart and the materials separate.”
This process takes place in a large pressure cooker-like device. “We feed the textiles into it, add a little alcohol and some base, and heat it up. After just over four hours of cooking, we open the lid, and the different fibers will have been separated.” This method promises a significant advancement in textile recycling, offering a practical solution to the current limitations in processing mixed-fiber fabrics.
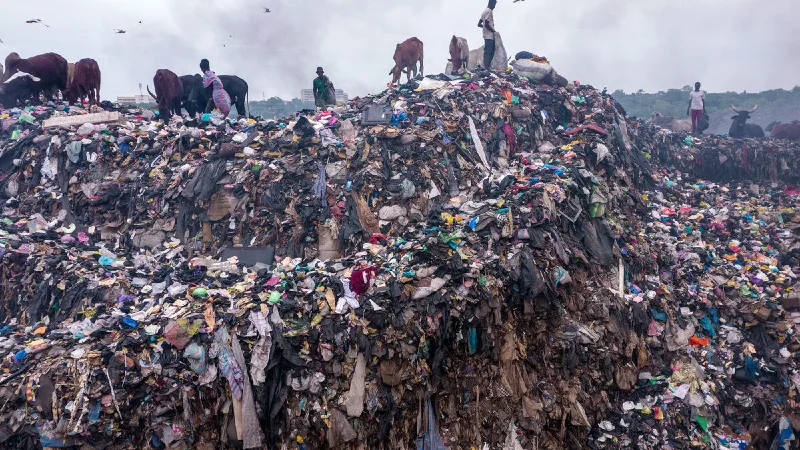
Elastane's Origins: A War-Time Invention
Elastane, the fiber that gives clothes their stretch, has an intriguing history that dates back to World War II. When Japan attacked Pearl Harbor on December 7, 1941, the U.S. faced a significant loss. Alongside the tragic loss of soldiers, aircraft, and ships, there was another critical setback – the loss of access to about 90% of their natural rubber supply.
Rubber was vital for the war effort, used in everything from vehicle tires to waterproof gear. To tackle this shortage, the U.S., following Germany’s lead, started producing synthetic rubber. This innovation wasn’t just a wartime necessity; it paved the way for a new era in synthetic materials.
The post-war era saw a boom in synthetic rubber production, leading to the discovery of several synthetic fibers for textiles, including elastane. In 1958, chemist Joseph Shivers made a groundbreaking invention – elastane, also widely known as Spandex in the United States. Since then, elastane has become a staple in our wardrobes, known for its exceptional elasticity and comfort.
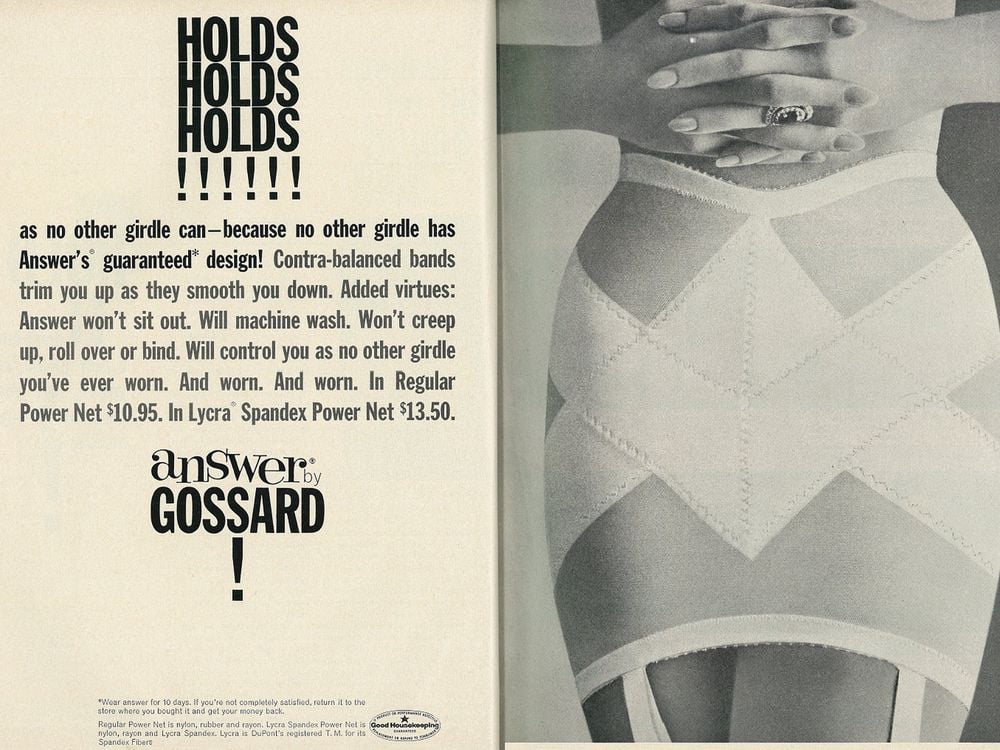
Elastane’s journey from a wartime innovation to a ubiquitous component in modern clothing is a testament to the ever-evolving nature of textile technology. Its widespread use today in various garments underlines its lasting impact and significance.
A Surprising Solution: Using Drain Cleaner to Recycle Fabric
In their quest to recycle mixed fabric fibers, Steffan Kvist Kristensen and his team have turned to an unexpected ingredient: drain cleaner. This choice is driven by the need to keep most of the fibers in clothes recyclable, ruling out the use of harsh chemicals.
The team’s approach involves using alcohol combined with a potassium hydroxide base, a common component in ordinary drain cleaners. “Potassium hydroxide is one of the main ingredients in ordinary drain cleaner. We found that adding this accelerated the process. It simply increases the speed of the chemical reaction,” explains Kristensen.
While the exact reason behind this acceleration isn’t completely understood, the effect is clear – it helps break the bonds in elastane. “We’re pretty sure that potassium hydroxide increases the reactivity of our alcohol. Either that, or the bonds are broken down slightly by the potassium hydroxide, so it is easier for the alcohol to break them completely,” he says.
This innovative use of everyday materials underscores the potential for practical, accessible solutions in the field of textile recycling. By leveraging the reactive properties of common substances like drain cleaner, the team has taken a significant step toward making fabric recycling more efficient and sustainable.
The Future of Textile Recycling: Here’s Looking At Germany!
The pioneering work of Steffan Kvist Kristensen and his team has shown great promise in recycling elastane-containing clothes. However, so far, their experiments have been limited to processing just two nylon stockings at a time. This means the technology isn’t ready yet for large-scale industrial use.
Scaling up is the next big challenge. “We can only scale things up a little because of the limitations in our equipment. So it’s up to industry to embrace the technology and scale it up in earnest,” Kristensen explains.
Denmark, despite being the birthplace of this technology, doesn’t have the capacity for large-scale implementation.
More To Discover
- Disassembly Lab Sneaker: Pioneering Sustainable Design in Footwear
- How Media’s Single-Use Mask Bias Contributed to PPE Pollution During The Pandemic
- San Diego Man Makes History as First in U.S. Charged for Smuggling Climate-Harming Gases
- Musk Lied About Using Terminally Ill Monkeys at Neuralink; They Died Horribly
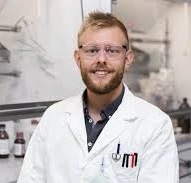
Kristensen looks towards Germany, known for its robust chemical industry, as a potential hub for adopting and expanding this technology. “The chemical industry in Denmark is small, but Germany has some of the largest plants in the world. They will most likely be able to use our method to recycle large amounts of fibers from elastane-containing clothes.”
For this technology to truly succeed and transform the textile recycling industry, it’s crucial for major chemical plants to see the value and potential profit in recycling and reusing materials. “If we’re to succeed with this, we need to get the large chemical plants on board. But they must see a business model in buying recycled materials and using them in the production of new fibers. If they don’t, the technology will never take off,” Kristensen emphasizes.
The future of sustainable fashion and textile recycling rests on the shoulders of industry giants. Their willingness to adopt and invest in such innovative technologies will determine whether these advances can make the leap from the lab to the global market.