Mining for aluminum, a process both essential and monumental in our tech-driven world, has for years been haunted by an unwelcome byproduct: vast quantities of red mud. This caustic sludge, a bitter remnant of the quest for aluminum, might just have found its moment of redemption.
Scientists, in a groundbreaking study published in Nature, have unveiled a simple yet innovative chemical process capable of extracting valuable iron from red mud and transforming the remaining substance into a benign material fit for concrete production.
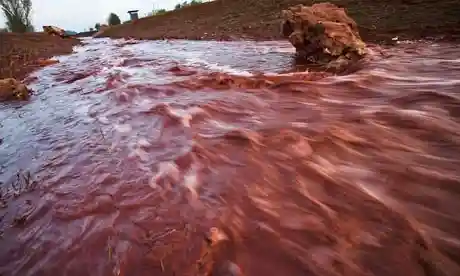
The implications are huge!
This method doesn’t just offer a way to salvage iron; it potentially paves the path for a more climate-friendly steel production. As Yiannis Pontikes, a mechanical engineer from KU Leuven, aptly puts it, the speed of the reactions and the purity of the product are “very promising.” However, he notes the caution needed since the experiment was conducted on only one type of red mud.
The journey of aluminum begins with mining bauxite, a rock abundant in aluminum oxide. The extraction of alumina leaves behind the notorious red mud – a highly alkaline, potentially toxic substance. It’s a growing environmental concern, with about 180 million tons generated annually and often stored in large reservoirs, posing significant risks.
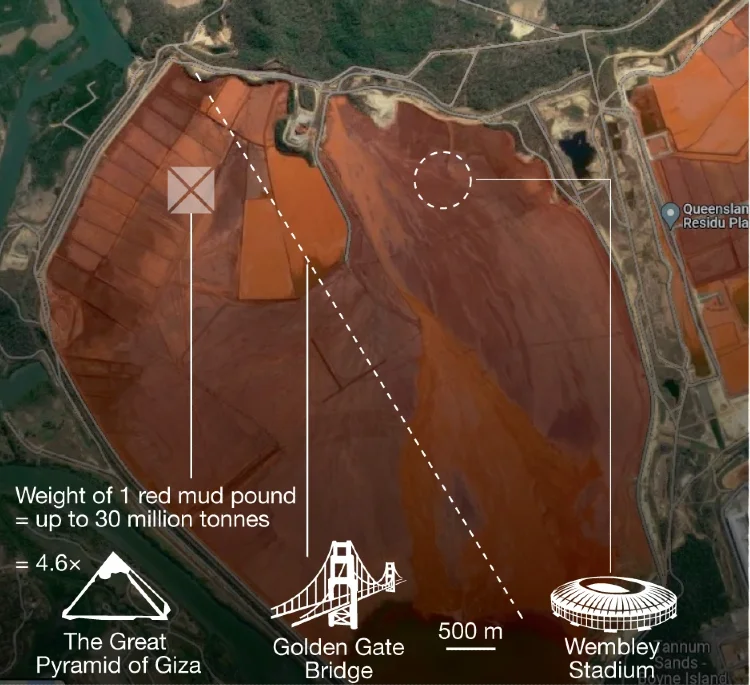
But red mud isn’t just a hazardous byproduct. It’s a treasure trove of iron, containing up to 70% of this metal by weight, along with smaller quantities of rare-earth metals like scandium.
The catch?
These valuable elements are trapped in oxides, making them less useful than their pure metal counterparts. The traditional method of reducing iron oxide to steel requires melting it with carbon, a process cheap and effective but heavy on fossil fuel use and carbon dioxide emissions.
Enter the game-changer: a process developed by Matic Jovičević-Klug and Isnaldi Souza Filho from the Max Planck Institute for Iron Research. By using an electric arc furnace and exposing red mud to a plasma of ionized hydrogen atoms, they’ve managed to strip oxygen atoms from the iron more efficiently than ever before. This technique, if powered by renewable energy, could revolutionize steel production.
The experiment’s success was somewhat unexpected, given red mud’s complex chemistry compared to iron ore. Yet, after melting a small amount of red mud in a furnace, the researchers were greeted with nearly pure iron spheres. “I was quite surprised,” admits Souza Filho. The process not only efficiently recovers iron but also neutralizes the pH of the leftovers, making them safer and cheaper for construction use.
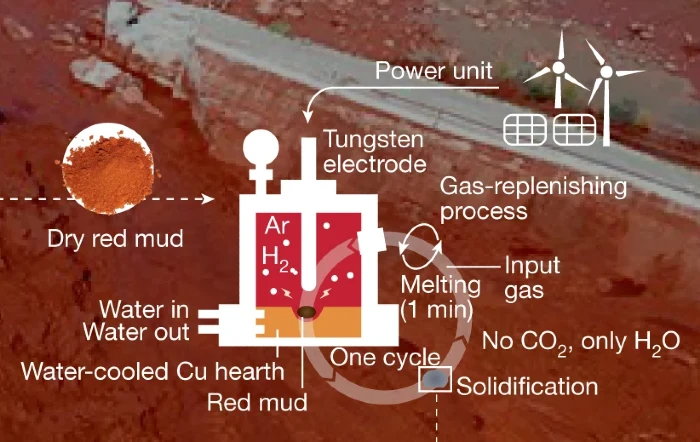
This innovative approach could lead to the production of hundreds of millions of tons of climate-friendly steel, significantly reducing the steel industry’s carbon footprint. The process’s simplicity is a major advantage, as it requires no pre-treatment of the red mud or the iron produced.
Chenna Rao Borra, a metallurgist at the Indian Institute of Technology Kharagpur, believes this could be a step toward the industry’s goal of reducing carbon emissions.
However, challenges remain. Pilot-scale studies are needed to assess economic viability and environmental impacts, including the management of fumes from the process. Large arc furnaces, typically used by steelmakers, might need to be constructed near red mud storage sites.
The feasibility of powering these furnaces with renewable energy sources, an aspect critical to the process’s climate-friendly claim, also requires consideration.
Alex King, a materials scientist at Iowa State University, points out that the success of this process hinges on the ore grade of the red mud and access to clean energy. Despite these hurdles, the potential of hydrogen plasma in transforming red mud from a problematic waste to a profitable resource is undeniable.
“I think it is all going to come down to the actual ore grade of the red mud that is most available and has the greatest access to clean energy,” King says. “It’s certainly a process worth looking at, within those constraints.” Alex King quote.
More To Discover
This breakthrough in red mud processing is more than just a technical advancement; it’s a beacon of hope in the quest for sustainable practices in the steel industry. It’s a testament to human ingenuity’s ability to find value in what was once considered waste, turning environmental challenges into opportunities for innovation and sustainable development.
Source: Nature