In an era of growing concerns over energy sustainability and climate change, the pursuit of nuclear fusion as a clean, near-limitless energy source has been a tantalizing prospect. Now, engineers at the University of Wisconsin-Madison have unveiled a groundbreaking technology that brings us one step closer to realizing the dream of commercial nuclear fusion reactors.
Nuclear fusion, the same process that powers our sun, holds immense promise as a clean energy solution. It involves the powerful collision of two atoms, merging them into a larger atom, while unleashing a vast amount of energy in the process. Unlike nuclear fission, which currently dominates the energy sector and leaves behind radioactive waste, fusion offers a cleaner, more efficient alternative. It produces three to four times more energy than fission and leaves no carbon footprint, unlike fossil fuel combustion. Additionally, fusion is inherently safe, with no risk of catastrophic nuclear meltdowns.
Make no mistake, currently, our present nuclear energy process is by far the most eco-friendly and environmentally responsible energy production source when compared to solar, wind, fossil fuels, coal, and everything else for that matter. But right now, no energy source is perfect! That will change the moment the mass production code on nuclear fusion is cracked!
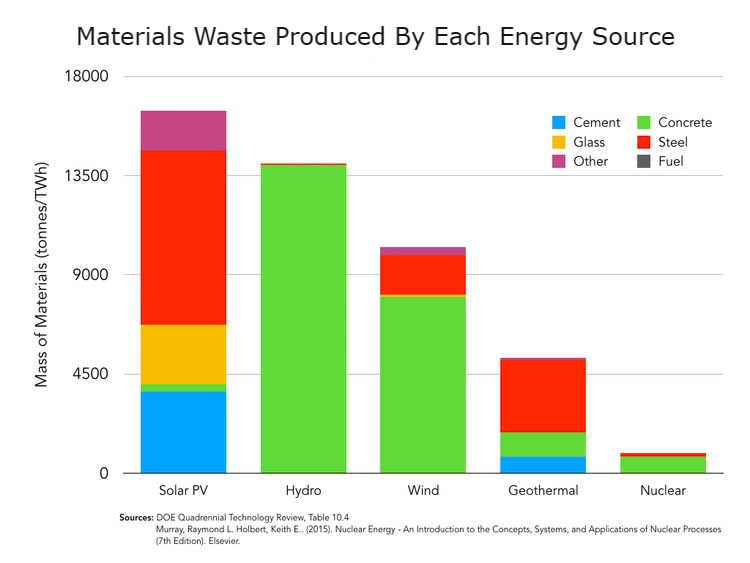
However, achieving nuclear fusion on Earth requires replicating the extreme conditions found in the heart of the sun, demanding colossal amounts of energy. In fact, the temperatures necessary for fusion to occur here are six times hotter than the sun’s core!
Under these blistering conditions, atoms enter a state known as plasma, a seething mix of negatively charged electrons and positively charged ions, torn apart by the intense heat. Typically, hydrogen atoms are used in fusion reactions. When superheated into plasma, these hydrogen atoms lose their lone electron, resulting in a mixture of positive hydrogen ions and free electrons. However, at the fringes of the plasma, where temperatures are lower, some hydrogen ions recombine with electrons, forming neutralized hydrogen particles.
This seemingly innocuous occurrence is a significant problem. These neutralized particles sap energy from the plasma, making it exceedingly challenging to sustain the high-temperature conditions essential for an effective fusion reaction. For a process reliant on energy efficiency, this issue is a formidable obstacle.
Mykola Ialovega, a postdoctoral researcher in nuclear engineering and engineering physics at UW–Madison, underscored the problem, stating, “These hydrogen neutral particles cause power losses in the plasma, which makes it very challenging to sustain a hot plasma and have an effective small fusion reactor.”
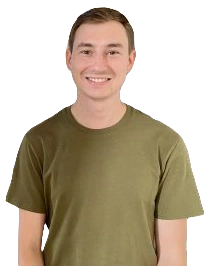
To overcome this hurdle, the UW-Madison team has devised an ingenious solution—a spray coating mechanism capable of trapping these problematic particles while enduring the brutal conditions within the nuclear reactor.
“The fusion community is urgently looking for new manufacturing approaches to economically produce large plasma-facing components in fusion reactors,” noted Ialovega.
The team’s innovation employs a cold spray process to apply a tantalum coating to the stainless steel interior of the reactor. Tantalum possesses exceptional resistance to the reactor’s extreme temperatures and excels at absorbing hydrogen.
Kumar Sridharan, a professor of nuclear engineering and engineering physics and materials science and engineering at UW-Madison, elaborated on the breakthrough, stating, “We discovered that the cold spray tantalum coating absorbs much more hydrogen than bulk tantalum because of the unique microstructure of the coating.”
Cold spray technology, akin to using a can of spray paint, involves propelling particles of the coating material onto a surface at supersonic speeds. Upon impact with the reactor walls, these particles flatten, akin to squashed M&Ms, forming a comprehensive coating. Crucially, tiny gaps persist between these particles, creating a larger surface area for hydrogen absorption.
Even more impressively, when subjected to higher temperatures, the material expels the trapped hydrogen, rendering it recyclable without the need to modify the coating.
The tantalum coating not only enhances reactor efficiency but also simplifies maintenance. Ialovega highlighted this advantage, explaining, “Currently, damaged reactor components often need to be removed and replaced with a completely new part, which is costly and time-consuming. Another big benefit of the cold spray method is that it allows us to repair reactor components on site by applying a new coating.”
Needless to say, this groundbreaking technology is a huge leap forward in fusion research and could sustainably power our species for the next 2,000 years, sustainably!
More To Discover
- Bosnia’s Seasonal River of Trash Is Back (Again) And The Predictable Plague Is Worse Than Ever
- Amazon’s Green Hope Reduced to Ash: Arson Devastates Three-Year Reforestation Endeavor
- Heat Pump Sales Stalled by Labor Shortage, Says Industry Experts
- Hydrogen in Maritime Shipping: Half-Truths Are Used To Keep The Green Hope Alive
“Our technology shows considerable improvements over current approaches. With this research, we are the first to demonstrate the benefits of using cold spray coating technology for fusion applications,” Ialovega proudly asserted.
The results of this pioneering research have been published in the journal Physica Scripta, heralding a brighter and more sustainable future for fusion energy.Â
As far as all of us at Dakoa are concerned, the mass production and scale of nuclear energy by fusion couldn’t arrive fast enough!