In Ashley, Indiana, at the heart of America’s heartland near a quaint water tower painted with a cheerful yellow smiley face, Brightmark Energy is attempting to pioneer a groundbreaking method known as ‘pyrolysis’ to tackle the global crisis of plastic waste. Which sounds amazing, hopeful even, but there’s a catch…many believe their process is the epitome of greenwashing.
The Controversial Technology Behind Pyrolysis
Pyrolysis, the process Brightmark is championing, aims to chemically decompose plastic waste at high temperatures in the absence of oxygen, transforming it into smaller molecules that can be repurposed as fuel. Proponents of this process like Jay Schabel, president of Brightmark’s plastics division, view it as a critical innovation that could solve our plastics crisis. Schabel, an electrical engineer, has dedicated the last 14 years to making this technology viable. He envisions plants like this dotted around the globe.
Schabel, during a tour of the facility which houses 900 tons of crushed plastic waste, shared his vision with palpable enthusiasm. “When I saw the technology, I said this is the sort of thing I can get out of bed and work on to change the world,” he remarked. The ambition is high, with plans for the $260 million, 120,000 square foot site to process 100,000 tons of plastic annually in a non-stop operation.
Sounds almost too good to be true, doesn’t it? Perhaps there’s a reason for that.
The plant’s operational start has been delayed multiple times since 2019, with the first commercial shipment of fuel to BP, originally scheduled for August of 2023, postponed to September and then further delayed, with full-scale operations now expected to stretch into 2024.
Critics argue that pyrolysis is energy-intensive, generates greenhouse gases, and essentially converts plastic waste into another form of dirty fossil fuel. Judith Enck, a former U.S. Environmental Protection Agency regional director and now leader of Beyond Plastics, voices a strong opposition: “The problem with pyrolysis is we should not be producing more fossil fuels,” she stated. “Using plastic waste as a feedstock for fossil fuels is doubling the damage to the environment because there are very negative environmental impacts from the production, disposal, and use of plastics.”
The United States grapples with inefficient recycling policies and a high rate of plastics ending up in landfills, incinerators, or polluting natural landscapes. And, of course, it’s not just the U.S. dealing with the plastics problem.
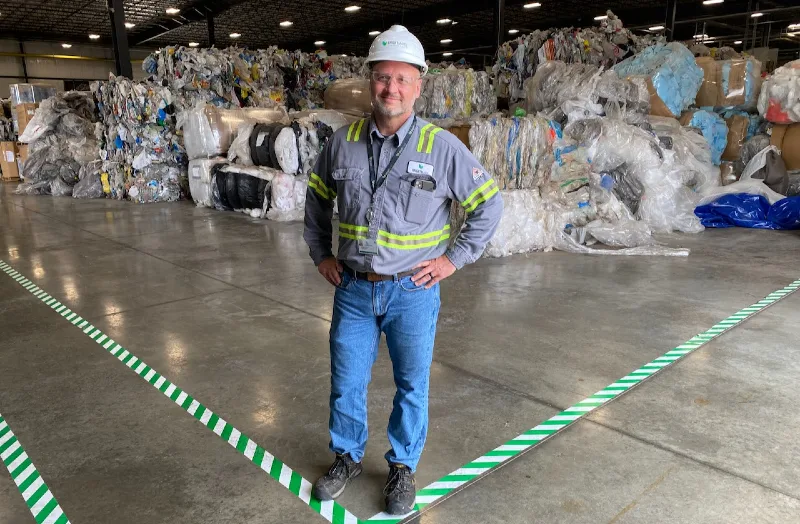
The Complex World of Plastic Recycling & The Plastic Crisis
The environmental catastrophe wrought by plastics is staggering, with global plastic production skyrocketing from 20 million metric tons in the past half-century to a colossal 400 million metric tons. These plastics, mostly made from fossil fuels, are notoriously resistant to biodegradation and just don’t decompose. In fact, a plastic bottle takes around 500 years to break down. And when plastics do start to break down, we’re left with something almost worse – microscopic fragments that have now pervaded every ecosystem, including the human body.
A grim forecast by a National Academies of Sciences, Engineering, and Medicine report in December warns that by 2030, the oceans could be inundated with up to 53 million metric tons of plastic annually. To put that into perspective, that’s nearly half the total weight of fish caught globally each year.
In the U.S. each person contributes nearly 300 pounds of plastic waste annually. A study by Beyond Plastics and the Last Beach Cleanup, based on recent EPA data, shows a dismal recycling rate—less than 6% of consumer-used plastics in the U.S. are recycled.
Traditional vs. Chemical Recycling
Traditional recycling processes like sorting, grinding, and melting primarily handle items such as soda bottles. But these processes have limitations. The variety of plastics they can manage and the number of times these plastics can be reused are limited.
In contrast, the chemical industry calls chemical recycling—and pyrolysis in particular—a near-miraculous solution that converts complex plastic waste back into basic chemicals. These chemicals are then used to produce a range of goods, from household detergents to automotive parts and clothing.
Pyrolysis: A Historical Process Reimagined for Modern Challenges
Pyrolysis, an ancient technique once used to produce tar and coke, involves heating plastic waste at high temperatures in an oxygen-deprived environment, sometimes with a catalyst, to break it down into synthetic gases, oil, and a carbon residue known as char.
Brightmark’s facility in Indiana, proclaimed as the largest-scale pyrolysis plant globally, aims to transform plastic waste into useful products. The plant processes plastic waste into pellets, which are then decomposed in pyrolysis tanks heated by burning natural gas. “We flush the molecules out and condense them,” Schabel explained. “We are hitting them with a thermal hammer to break them into pieces. They want to come back together, but we control how they come back together.”
The output includes low-sulfur diesel, naphtha, and wax, which are further refined on-site. Schabel describes the operation as a “hyper-local oil well,” a sustainable twist on traditional oil production.
Concerns Over Efficiency and Environmental Impact
The process is far from efficient. Brightmark’s own reports to the EPA proved that only 20% of the plant’s output comprises its primary products, like fuel. The rest includes synthetic gas used to generate heat (70%), with 20% of this gas flared off. The company has since disputed their own figures, by saying that they’re working to correct them for a higher output of diesel and naphtha.
Yet, the very nature of pyrolysis has drawn sharp criticism for not truly being a form of recycling – which it isn’t.
“With pyrolysis, what you make is what I would call, and I grew up in New Jersey, so forgive me, a dog’s breakfast of compounds,” said Professor Eric Beckman from the University of Pittsburgh. He points out the mixture of gases, liquids, and solids produced and the significant energy required to achieve high temperatures as major flaws.
Jan Dell, a chemical engineer, and advocate for The Last Beach Cleanup, shares these concerns, noting the excessive burning required in pyrolysis processes. “The fact that pyrolysis operations have to burn so much of the material to get to the high temperatures is a fundamental flaw,” she stated.
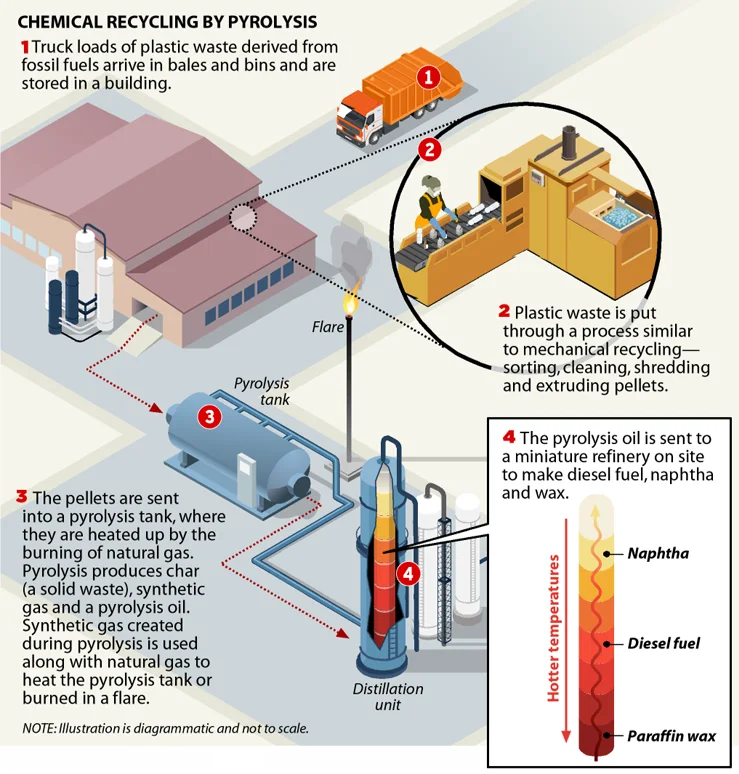
The EPA’s Deliberation on Pyrolysis
The EPA has traditionally classified pyrolysis as a form of incineration due to its use of high heat to decompose materials, necessitating stringent air pollution controls. However, this perspective began to shift during the late stages of the Trump administration when the EPA proposed a rule change suggesting that pyrolysis shouldn’t be considered combustion and therefore not subject to the same regulations as traditional incineration. Of course, this was after a considerable amount of industry lobbying.
In mid-July, a group of 35 legislators, including Representative Jamie Raskin and Senators Bernie Sanders and Cory Booker, penned a letter to the EPA. They urged the agency to maintain stringent regulations on emissions from chemical recycling processes, emphasizing the potential environmental and public health risks.
“Chemical recycling contributes to our growing climate crisis and leads to toxic air emissions that disproportionately impact vulnerable communities,” the lawmakers argued in their letter. This stance reflects growing concerns over the environmental justice implications of expanding chemical recycling operations, particularly in communities already burdened by pollution.
Industry and Environmental Advocates Weigh In
Joshua Baca, Vice President of Plastics for the American Chemistry Council, emphasizes the importance of appropriate regulatory measures: “The appropriate regulation of this is really critical if you want to scale advanced recycling, and you want to use more recycled material in your products,” he stated. This view highlights the industry’s push for regulatory adaptations that would facilitate the expansion of chemical recycling technologies like pyrolysis.
On the other side of the matter, critics argue that even if pyrolysis does not involve traditional combustion, it still ultimately burns plastic, albeit indirectly.
James Pew, an attorney and director of Earthjustice’s clean air practice, points out that facilities using pyrolysis often burn the gases produced to generate the heat necessary for the process itself, involving some level of oxygen and thereby linking back to combustion. “The absolute crux of this issue is whether these new incinerators have to put on controls, like with conventional incinerators, or whether they can skip that and not control or monitor their pollution,” Pew explained.
Operational Challenges and Technological Hurdles at Brightmark
At the end of July, Bob Powell, the Chief Executive Officer of Brightmark, detailed the ongoing efforts to optimize the company’s innovative plastic recycling process during a Zoom interview from his office in San Francisco. “We have operated it at startup levels,” Powell noted, emphasizing that the plant has only recently achieved mechanical completion and is beginning to produce its intended finished products.
Financial and Developmental Milestones
The journey for Brightmark began in earnest in 2019 with a groundbreaking ceremony, following the acquisition of a $260 million financing package. This package included $185 million in bonds issued through the Indiana Finance Authority and underwritten by Goldman Sachs. It’s important to note that the financing doesn’t constitute state debt, leaving Brightmark fully responsible for repayment, which should any Indiana taxpayers, reading this, feel better.
Despite the ambitious start and plump bank account, the company has faced significant delays. Jay Schabel, during a tour of the facility, candidly acknowledged the challenges—from securing a consistent supply of plastic waste to operational delays caused by the Covid pandemic and the hurdles inherent in pioneering new technologies.
The Complex Reality of Recycling Mixed Plastics
Jan Dell, a consultant and advocate with The Last Beach Cleanup, expressed skepticism regarding Brightmark’s ability to manage the diverse and contaminated stream of plastic waste it targets. The company aims to recycle mixed, post-consumer plastics—commonly found in household recycling bins—which consist of various types of plastics with different chemical properties.
According to Dell, these variations introduce complications. For example, certain plastics release oxygenated molecules during the pyrolysis process, reducing yield and degrading the quality of the resulting pyrolysis oil. Particularly problematic is Polyvinyl chloride (PVC), found in many consumer products, which releases chlorine atoms that can corrode processing equipment and contaminate the final products. Furthermore, municipal plastic waste often comes mixed with other types of refuse like food, metal, and glass, which can further disrupt the pyrolysis process.
“There’s this perception that there’s so much plastic waste in the world and in the country, which there is,” Dell stated. “And then they hold up this magic plant that they say is going to recycle everything from households all mixed together, and people believe it. But it can’t. It can’t handle the changing variety of household plastic waste and the unavoidable contamination.”
Addressing the PVC Challenge
Eric Beckman from the University of Pittsburgh expressed particular concern about the inclusion of PVC in the recycling process, given its potential to produce harmful byproducts like dioxins—known to be persistent organic pollutants and potential carcinogens. “I do not know how they’re taking in PVC, and not getting something you really don’t want,” he remarked, highlighting the risks associated with recycling this type of plastic.
Despite these concerns, Schabel remains confident in the plant’s capability to handle such challenges through its proprietary technology, initially developed by RES Polyflow, where he previously served as CEO. While he refrained from detailing the technology, he noted that strategically removing more PVC from the waste stream could improve overall yield.
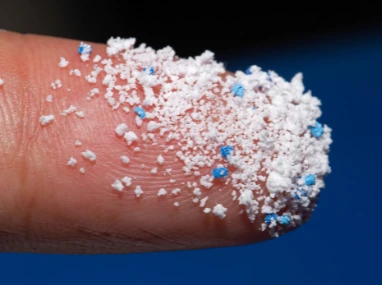
Between Green Solutions and Greenwashing: Marketing Meets Environmental Science
Brightmark’s efforts to position its Ashley plant as a green solution to the escalating global plastic and climate crises is not just about innovative technology, but also about strategic marketing.
The company, which is diversifying into manure-to-gas projects around the U.S., describes the Ashley facility as a “plastics renewable facility.” This branding is supported by an environmental lifecycle analysis commissioned from Environmental Clarity, Inc.
The analysis suggests that the pyrolysis process at the plant could offer significant environmental benefits. Specifically, it found that the plant produces 39 percent fewer greenhouse gas emissions compared to traditional methods where 17 percent of plastic waste is incinerated, and products are made from virgin materials.
Critiques of the Lifecycle Analysis
However, Terrence Collins, a professor of green chemistry at Carnegie Mellon University, expresses skepticism about the study’s conclusions. Collins pointed out that the analysis relies heavily on assumptions and lacks comprehensive environmental impact considerations, such as emissions of toxic chemicals including dioxins and endocrine disruptors—substances that can interfere with hormonal systems and potentially cause reproductive and developmental issues.
“I did not see a single measurement for dioxin, or even talking about it,” Collins noted. He also highlighted the absence of terms like ‘endocrine disruption’ and ‘health’ in the report, suggesting that the study might be overlooking significant environmental and health impacts.
Accusations of Greenwashing
Collins’s concerns extend to the way Brightmark markets its technology, particularly its use of imagery involving children playing with plastic toys and discussing the prevention of ocean dumping of plastics. “It’s greenwashing up the wazoo,” Collins remarked, criticizing the company for using emotional appeals without sufficiently backing its claims with science. “If you market through children, you raise the stakes; you really need to prove it,” he added.
In response to these concerns, Evan Griffing, co-author of the lifecycle analysis, defended the scope and conclusions of the study, noting that it was defined by Brightmark. Griffing acknowledged the well-known risks of dioxin production in processes like incineration and pyrolysis but mentioned that controlling the temperature and minimizing chlorine input, such as by scanning for and excluding PVC, can mitigate these risks.
Despite criticisms, the study’s authors, Griffing and Michael Overcash, assert that Brightmark’s technology “reduces fossil fuel extraction, reduces landfill and incineration of waste, and cuts down carbon emissions relative to current practice.” They believe that scaling such advanced recycling technologies can provide substantial environmental and sustainability benefits.
However, the numbers within the lifecycle analysis revealed that only 16 percent of the plastic waste entering the plant and 20 percent of the sorted input to the pyrolysis process is converted into naphtha, a key feedstock for new plastics. Despite this, Chrystal Boone, a Brightmark vice president, maintains that the technology offers significant benefits over the disposal methods that currently handle most post-use plastics.
More To Discover
- Science Class or Beef Commercial? How the Beef Industry is Targeting Your Kids’ Classrooms
- Trees Are The Unexpected Climate Challengers on the Great Plains
- Governments Spend $22 Billion A Year To Accelerate Overfishing (11 Countries Spending The Most)
- The Bioengineered Plant Battling Indoor Air Pollution
Brightmark’s Setbacks and Strategic Shifts
Brightmark’s vision for a sustainable future faced a significant setback earlier this year due to operational delays at its Ashley, Indiana plant. These challenges have had repercussions beyond state lines, impacting the company’s expansion plans in Georgia.
Last year, Brightmark attempted to establish a second, larger pyrolysis plant in Macon, Georgia. This ambitious project was supported by a proposed $500 million in bonds from a local development authority. However, the deal fell through in April when Brightmark failed to demonstrate its capability to deliver end-products from its Ashley facility, as reported by local and national media.
The collapse of the Macon deal has been perceived by environmental advocates both locally and nationally as a victory, potentially stalling what they saw as the beginning of a broader rollout of Brightmark’s technology.
Despite these setbacks, Brightmark is not retreating. Bob Powell, CEO of Brightmark, described the situation in Macon as “unfortunate” but remains optimistic about finding new locations in the Southeast. His immediate focus, however, is on getting the Ashley plant fully operational.
Jay Schabel, sharing Powell’s forward-looking attitude, expressed a desire to address the criticisms head-on. “I want to bring the critics in and show them,” Schabel stated, indicating his hope to demonstrate the plant’s capabilities and its environmental benefits in practice.
In conclusion, as the discussion about the future of plastic waste management continues, the role of innovative technologies like pyrolysis and the broader concept of chemical recycling remain pivotal. Brightmark’s experiences in Ashley and beyond underscore the complexities and challenges of implementing new solutions in an area fraught with environmental, technical, and regulatory hurdles.