In a substantial stride toward sustainability, scientists have cracked the code on recycling one of the most prevalent yet stubborn plastics plaguing our planet. The material in question, low-density polyethylene (LDPE), is everywhere—from grocery bags to squeeze bottles, its footprint is inescapable. Yet, its complex chemical makeup has long rendered it a recycling nightmare. That is, until now.
At the heart of this revolutionary breakthrough is Prof. Dr. Rhett Kempe and his interdisciplinary team from the University of Bayreuth’s Sustainable Chemistry Center. Their research, heralded in the pages of the journal Advanced Science, doesn’t just edge us closer to a solution; it catapults us into a future where LDPE doesn’t have to be a choice between utility and the environment.
A Leap Towards Chemical Recycling
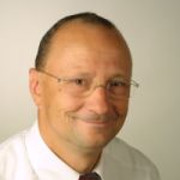
“We have introduced a new chemically recyclable, highly branched polyolefin material,” states Prof. Dr. Kempe with a tone that marries excitement with the gravitas of the achievement. What makes this innovation stand out is the introduction of “recycling points” within the plastic’s structure.Â
These points act as molecular disassembly lines, where the polymer is broken down into smaller, organically soluble fragments at relatively mild temperatures. The beauty of it? These fragments can then be reassembled, reborn to serve anew in a perfect cycle of sustainability.
The traditional production of LDPE is a high-stakes, energy-guzzling affair, requiring temperatures of 250°C and pressures between 2,500 to 4,000 bar. This intensive process is what gives LDPE its desirable, yet recycling-resistant, highly branched structure. The challenge of replicating this unique structure has been a significant barrier—until Kempe’s team’s LDPE-mimic came along, boasting a chemical structure strikingly close to its commercial counterpart.
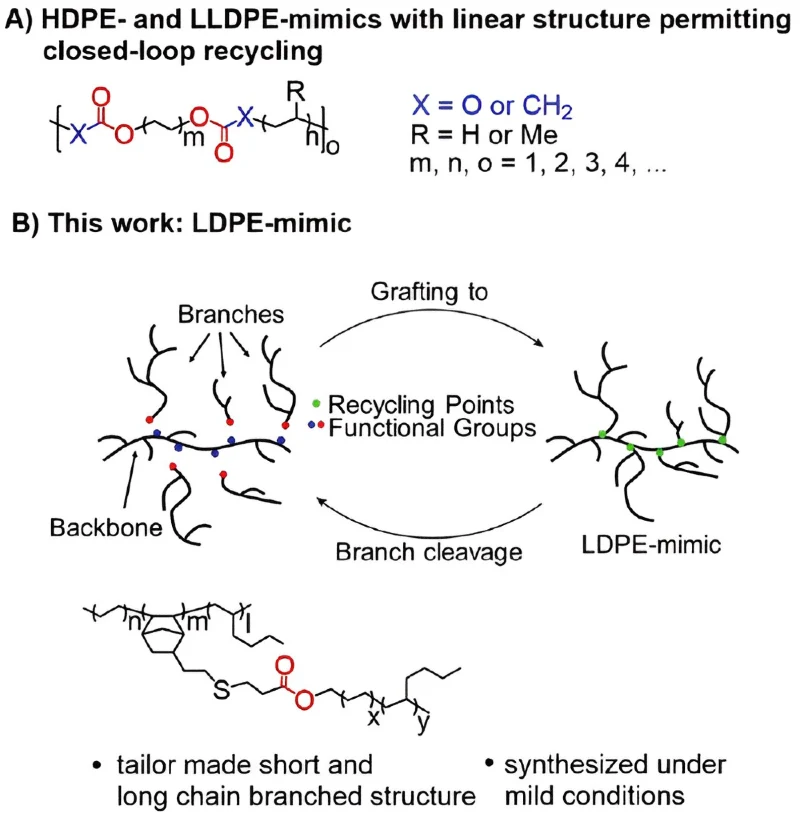
The Catalyst of Change
At the core of this breakthrough is a novel set of catalysts designed by Kempe’s team. These catalysts are the magicians, enabling the creation of defined building blocks at the much gentler conditions of 70° Celsius (158 degrees F) and two bar pressure. These building blocks are the foundation of the final, recyclable plastic material.Â
“The new material consists of two different macromonomers, a backbone and potential long-chain branches. The branches can be reversibly attached to the backbone and cleaved under acidic and basic conditions,” Kempe explains. This flexibility and reversibility mark a monumental leap in plastic production and recycling technology.
Beyond the Lab
The implications of this discovery stretch far and wide. For an industry under increasing pressure to reduce its environmental footprint, this method offers a beacon of hope.
Not only does it promise a reduction in the energy-intensive processes currently dominating plastic production, but it also heralds a future where plastic can be perpetually recycled without degrading its quality or usability.
The innovation aligns perfectly with global efforts to combat plastic pollution, offering a practical solution to one of the most pressing environmental challenges of our time.
The work of Prof. Dr. Kempe and his team is more than just scientific excellence; it’s a testament to the power of human ingenuity in the face of environmental crises. It underscores the possibility of a future where the materials we rely on daily don’t have to cost the earth.
More To Discover
- UK Launches Investigation into Dove Parent Unilever’s Green Claims
- Logitech Tackles Plastic Waste By Switching To Ancient Material
- What Happens When There’s Less Wind To Power Our Turbines? Illinois’ Is Dealing With That Now.
- MIT’s Bacteria-Based Solution for Sustainable Farming May, One Day, Replace Chemical Fertilizers
As this research progresses and hopefully transitions from the laboratory to industry, the dream of a circular plastic economy inches closer to reality. In this future, the phrase “throw-away culture” might just become a relic of the past, as we embrace materials designed not just for use, but for reuse, time and time again.
Source: Advanced Science